Comprehensive Guide on Cost Control Through Standard Costing – Techniques | Variance Analysis | Insights
- Other Laws|Blog|
- 24 Min Read
- By Taxmann
- |
- Last Updated on 9 February, 2024
Table of Contents
- Historical Costing
- Standard Cost and Standard Costing
- Types of Standards
- Setting of Standards
- Standard Cost for Direct Material
- Standard Cost for Direct Labour
- Standard Costs for Overheads
- Standard Hour
- Important Terminology in Standard Costing
- Prerequisites for Establishing Standard Costing System
- Standard Cost and Estimated Cost: Distinction
- Setting of Standards During Inflation
- Responsibility for Setting Standards
- Standard Costing and Budgetary Control: Distinction
- Standard Costing and Budgetary Control: Interrelation
- Problems in Setting Standards
- Advantages and Limitations of Standard Costing System
- Reasons for Growing Importance of Overheads
- Non-Compatibility of Standard Costing with Activity Based Costing
- Behavioural Considerations in Standard Costing
- Meaning of Variance Analysis
Check out Taxmann's Strategic Cost Management which presents an in-depth discussion of cost management in the contemporary business landscape. It covers traditional and modern techniques across 38 chapters, with a special emphasis on Operations Research, making complex topics like Simulation Modeling and Linear Programming more digestible. Tailored for students and professionals in advanced cost management studies, this book stands out for its simple language, illustrative diagrams, and practical problem-solving approach. It's a vital resource for those pursuing M.Com., MBA, MFM, CA, CMA, and CS courses, blending theoretical and practical learning.
1. Historical Costing
1.1 Meaning
In this type of costing system, costs are ascertained only after they have been incurred. It is the process of accumulation of costs after they are incurred in a systematic manner. The amounts spent on material, labour and overheads are recorded and these expenses totalled together give a figure of cost of providing a particular product. The historical costs are used only for postmortem examination of actual costs incurred and it would be too late to control.
1.2 Limitations
The historical costing suffers from the following limitations:
(a) Costs are known after they have incurred, which is not useful for taking corrective action in time.
(b) Historical cost records does not provide for cost comparison, due to changes in business environment and situation.
(c) It is very expensive to maintain detailed cost records
(d) It will be duplication of financial accounting records.
(e) The historical cost data will not be much useful in taking crucial decisions like price fixation, adoption of responsibility accounting concept, budgeting etc.
(f) Historical cost data is always available late, which may not be much useful for even taking managerial decisions.
(g) It does not help for future financial planning.
(h) It is not preceded by planned costs which are a must for effective cost control.
1.3 Emergence of Standard Costing
Historical cost accounting is not considered sufficient to supply required information for taking managerial decisions. The emphasis of management on using cost as control device has brought the emergence of Standard costing. The technique of standard costing has been developed because of change in emphasis from cost ascertainment to cost control. Standard costing is a technique which helps management to control costs and business operations. It aims at eliminating wastes and increasing efficiency in performance through setting up standards or formulating cost plans.
2. Standard Cost and Standard Costing
2.1 Standard
The word ‘standard’ means a benchmark or yardstick. A standard is a predetermined measurable quantity set in defined conditions against which actual performance can be compared, usually for an element of work, operation or activity.
2.2 Standard Cost
The standard cost is a predetermined cost which determines in advance what each product or service should cost under given circumstances. Standard cost is the amount the firm thinks a product or the operation of a process for a period of time should cost, based upon certain assumed conditions of efficiency, economic conditions and other factors. A standard cost is a planned cost for a unit of product or service rendered. Standard costing is universally accepted as an effective instrument for cost control in industries. The predetermined costs based on technical estimate of material, labour and overhead for a selected period of time and for a prescribed set of working conditions.
2.3 Standard Costing
Standard costing involves the setting of predetermined cost estimates in order to provide a basis for comparison with actual costs. Standard costing is a technique which uses standards for costs and revenues for the purpose of control through variance analysis. Standard costing is a technique of cost accounting which compares the standard cost of each product or service with actual cost to determine the efficiency of the operations so that any remedial action may be taken immediately. Standard costing means the preparation and use of standard costs, their comparison with actual costs, and the analysis of variance to their causes, and points of incidence.
Standard costing is a system of cost accounting which is designed to find out how much should be the cost of a product under the existing conditions. The actual cost can be ascertained only when production is undertaken. The predetermined cost is compared to actual cost and a variance between the two enables the management to take necessary corrective measures. Although the terms budgeted and standard costs are sometimes used interchangeably, budgeted costs normally describe the total planned costs for a number of products.
2.4 Suitability
Though standard costing system will be useful for all types of commercial and industrial undertakings but it will be more useful in those undertaking where production is standardized. With the use of standard costing the organization achieves the objectives in a planned and systematic manner. Standard costing can be used in direct costing, absorption costing, unit costing and process costing. It is not a method of costing but a system which can be fitted in any method. It will be of less use in Job costing system because every job has different specifications and it will be difficult to determine standard costs for every job.
2.5 Features
The important features of standard costing system are as follows :
- Predetermine the standard costs.
- Establish inputs for outputs.
- Make it applicable to all routine aspects of an organization’s operations.
- Recording of actual cost.
- Comparison between standard cost and actual cost.
- Finding out variance.
- Reporting of variance to management for taking appropriate action wherever necessary.
2.6 Objectives
The implementation of standard costing will fulfil the following objectives :
- To provide a formal basis for assessing performance and efficiency.
- To control costs by establishing standards and analysis of variances.
- To enable the principle of ‘management by exception’ to be practised at the detailed, operational level.
- To assist in setting budgets.
- To enable standard costs as readily available substitutes
- To assist in assigning responsibility for non-standard performance
- To motivate staff and management.
- To provide a basis for estimating.
- To provide guidance on possible ways of improving performance.
3. Types of Standards
3.1 Current Standard
It is a standard established for use over a short period of time, related to current conditions. It reflects the performance which should be attained during the current period. The period of current standard is normally one year.
Assumption – It is presumed that conditions of production will remain unchanged during the period. In case there is any change in price or manufacturing conditions, the standards are also revised.
Disadvantage – The problem with this type of standard is that it does not try to improve on current levels of efficiency.
Classification – The current standard may be (i) ideal standard or (ii) expected standard.
3.2 Ideal Standard
It is a standard which can be attained under the most favourable conditions. This represents a high level of efficiency. No provision is made, e.g., for shrinkage, spoilage or machine breakdowns. This is the standard based on the maximum efficiency under the most favourable conditions possible.
Assumptions
- It is fixed on the assumption that favourable conditions will prevail and management will be at its best.
- It is assumed that there is no wastage, no ideal time, no inefficiencies or other imperfections in the manufacturing process.
- Both, internal and external, conditions should be favourable and only then ideal standard will be achieved.
Disadvantages
- Ideal standard is fixed on the assumption of those conditions which may rarely exist.
- This standard is not practicable and may not be achieved.
3.3 Expected Standard
This standard is based on the expected conditions. It is the target which can be achieved if expected conditions prevail. It can be attained if a standard unit of work is carried out efficiently, on a machine properly utilized or material properly used. Allowances are made for normal shrinkage, waste and machine breakdowns. All existing facilities are taken into consideration and expected changes are also taken into account while fixing the expected standard. An allowance is given for human error and normal deficiencies in fixing this standard. The expected standard is more realistic and attainable.
Disadvantage – This standard requires constant revision, otherwise the standard will be meaningless.
3.4 Basic Standard
It is a standard established for an indefinite period which may be for a very long period from which a current standard can be developed. It is not adjusted to the present conditions. These standards are revised only on the changes in specification of material and technology of production process.
Advantage – It shows changes in trend of price and efficiency from year to year.
Disadvantage
- It has remained unaltered over a long period of time, it may be out of date.
- It is based on perfect performance which is rather impossible to attain.
- The deviation between standard cost and actual cost cannot be used as a yardstick for measuring efficiency.
3.5 Normal Standard
It is the average standard which is anticipated and can be attained over a future period of time, preferably long enough to cover one trade cycle. Such standards are established on the basis of average estimated performances with reasonable degree of accuracy for a long period of time. It is a standard fixed based on average performance in the past. Past may contain details of inefficient performance.
Disadvantage
- A standard evolved on this basis is also not good for standard costing purposes.
- It may not be a useful device for the purpose of cost control.
4. Setting of Standards
4.1 Production Standard
Study of the technical and operational aspects of the manufacturing processes and methods etc. Review of existing costing system, cost records and forms in use. Decide the type of standard to be used. Based on the factors as stated above, the production and cost standards are to be set up.
4.2 Cost Standard
Proper classification of accounts is a must so that the cost variances could be correctly accounted for. Reliability and accuracy of cost standards are the prerequisites for the success of standard cost system. Fixation of responsibility for setting cost/price standards and coordinate the complete work of establishment of standard costing system.
4.3 Precautions
- Standards have to be set for each element of cost for each line of product manufactured or service supplied.
- Standard cost shows what the cost should be keeping in mind the most favourable production conditions, and on the assumption that plant will operate at maximum possible efficiency.
- The collaboration of all functional departments is a must in setting standards.
- The quantities, price and rates, qualities or grades, terms of purchase, product substitution etc. have to be kept in mind while setting standards.
- In order to enable an organization to setup or install standard costing system the management has to finalize and prescribe various forms, methods and systems, keeping in mind the nature, size and technicalities of the business and motivate responsible persons.
4.4 Considerations
- Standard setting should be sufficiently refined to provide adequate information.
- Both quantitative and qualitative information should be given proper attention.
- Standard costing system should provide for opportunity costs and profit forgone.
4.5 Persons Involved
Production manager and Cost accountant should work together in setting up the production standards and for the establishment of standard costs. Production manager should determine the quality and quantity standards. The Cost accountant should work out for the cost, price and usage standards.
5. Standard Cost for Direct Material
The setting of standard for direct material involves two things:
5.1 Quantity of Materials
Before determining the quantity of materials, the quality and size of materials should be determined. The standard quality to be maintained should be decided. The quantity and quality of materials should be decided by the Engineering department by making used of historical data. An allowance for changing conditions should also be given for setting standards. While setting quantity standards, a proper consideration should be given to normal material wastages. For this purpose, a number of test runs may have to be carried out to decide on normal process losses. Quantity usage standards are set on the basis of various test runs and guidelines provided by R&D department or Engineering department and specifications on the basis of past experience. The standards should also take into consideration allowances for acceptable level of waste, spoilage, shrinkage, seepage, evaporation, leakage, etc.
5.2 Price of Materials
Price factor is controlled by external factors. The standard cost of materials will be decided in consultation with the purchase department. The cost of purchasing and storing of materials and inventory carrying costs should be taken into consideration. The factors like levels of inventory, discount policy, means of transport, cost of ordering material and follow-up, inventory carrying costs etc. should be considered before fixing price standard of materials. The expected future price changes should be anticipated while setting up standard price. If the price changes during the period due to inflation, raise in prices of controlled items like cement, steel, etc., there is going to be wide variations. Material prices are fixed keeping in mind the terms of contract of purchase, nature of items and other relevant factors. Some organizations have regular system of purchases (rate contract) for the whole period/year at predetermined price irrespective of prevalent market rates.
6. Standard Cost for Direct Labour
The setting of standard for direct material involves two things:
6.1 Standard Labour Time
Standard labour time indicates the time taken (hours) by different categories of workers for performing a particular job. The general principles followed for setting standard labour time will include past performance records, test run result, work study etc. The labour efficiency means the number of hours that the appropriate grade of worker will take to perform the necessary work. It is based on actual performance of worker or group of workers possessing average skill and using average effort while performing manual operations or working on machine under normal conditions. The standard time is fixed keeping in mind past performance records or work study. This is on the basis that is acceptable to the worker as well as the management.
6.2 Labour Rate Standard
The labour rate standard refers to the expected wage rates to be paid for different categories of workers. The anticipation of expected changes in labour rates will be an essential factor. In case there is any agreement with the workers for payment of wage rates in the coming period then these rates should be used. If a premium or bonus scheme is in operation then anticipated extra payments should also be included. Where a piece rate system is used the standard cost will be fixed piece rate. This is basically dependent on the agreement with the labour unions or rate prevalent in the particular area or industry. The labour rate depends on different grades of labour.
7. Standard Costs for Overheads
The purpose of setting overhead rates is to minimize overhead costs. The standard overhead rates are computed by dividing overhead expenses by direct labour hours or units produced. The standard overhead cost is obtained by multiplying standard overhead rate by the labour hours spent or number or units produced. The overheads are classified into fixed and variable overheads for computation of variances. It is necessary to determine the level of activity, based on that the amount of overhead will be calculated. The estimation on activity level will enable to determine the estimated production in units or labour hours spent. The overhead rates are determined with the following formula:
Standard Variable Overhead Rate = Budgeted Variable Overheads for Budget Period/Budgeted Production in Units or Budgeted Hours for Budget Period
Standard Fixed Overhead Rate = Budgeted Fixed Overheads for Budget Period/Budgeted Production in Units or Budgeted Hours for Budget Period
8. Standard Hour
In a business organization where only single product is manufactured, produced or dealt, it is simple to identify costs with that single product. But when a concern manufactures different varieties of products, it is difficult to aggregate production expressed in different units. To eliminate this difficulty, the production is expressed in a common measure called ‘standard hour’. A standard hour is a hypothetical hour representing the amount of work which should be performed in an hour under standard conditions. The standard hour is a unit of work and not of time. The quantum of work done in one hour is known as ‘standard hour’.
Example
A furniture company manufactures different varieties of products like Single bed cots, Double bed cots, tables, chairs, cabinets etc. The computation of standard hours of those products are illustrated as below:
Products |
Standard Hours per unit | Quantity Produced |
Output in Standard hours |
Single cot beds | 15 | 400 | 6000 |
Double cot beds | 22 | 600 | 13,200 |
Tables | 8 | 1000 | 8000 |
Chairs | 5 | 1500 | 7500 |
Cabinets | 9 | 650 | 5850 |
9. Important Terminology in Standard Costing
The terminology used by CIMA, London on Standard costing systems are summarized as follows:
Standard Hour/Minute: The quality of work achievable at standard performance, expressed in terms of a standard unit of work in a standard period of time.
Standard Time: It is the total time (hours and minutes) in which a task should be completed at standard performance i.e., basic time p/us contingency allowance p/us relaxation allowance.
Standard Unit of Work: It is a unit of work consisting of basic time p/us relaxation allowance and contingency allowance where applicable. The unit of work may be for labour output only, a combination of machine and labour output, or for a machine only.
Standard Performance of a Machine: It is the rate of output achievable by a machine on an average, under specified conditions over a given period of time. It may include the standard performance of the operator.
Standard Direct Material Cost: It is the predetermined cost price for a specified quality of material to be used at a standard material usage rate over a specified period.
Standard Material Usage: Standard material usage is the quantity of material or rate of use required as an average, under specified conditions, to produce a specified quantity of output.
Standard Direct Labour Cost: It is the planned average cost of direct labour for a specified amount of direct labour effort to be used at standard performance over a specified period. It is usually expressed as a cost per unit of time i.e., standard hour or standard minute.
Standard Overhead Cost: It is the predetermined cost of overhead of a cost/revenue/profit centre over a specified period, using an agreed overhead absorption method. In Marginal costing, this will be in respect of variable overhead only.
Standard Performance – Labour: It is the rate of output which qualified workers can achieve on an average over the working day or shift, without over exertion, provided they adhere to the specified method and are motivated to apply themselves to their work.
Standard Production Cost – Total: It is the predetermined cost of producing or providing specified quantities of products or service at standard performance over a specified period.
Standard Production Cost – Unit: It is the predetermined cost of producing or providing specified quantity of a product or service at standard performance.
Standard Selling Price – Unit: It is a predetermined price for a product or service for a specified unit to be sold. A unit may consist of a single item or a batch of processed output.
Standard Price: It is a predetermined price fixed on the basis of specification of a product or service and of all factors affecting that price.
Standard Operating Profit – Unit: It is the predetermined profit from the sale of a specified unit of a product or service at the standard selling price.
Standard Profit – Total: It is the predetermined profit arising from the sale of actual quantities of products or services at standard selling prices, over a specified period.
Formula: Actual number of units sold × (Standard selling price p.u. – Standard cost p.u.)
Standard profit may be at the level of net profit, gross profit or combination. Profit which relates only to trading activities is often referred to as ‘operating profit’.
10. Prerequisites for Establishing Standard Costing System
The establishment of a standard costing system involves the following steps:
- Determination of Cost Centres – Cost centres are necessary for determining the costs. Cost centres enable the determination of costs and fixation of responsibility.
- Classification and Codification of Accounts – Classification of accounts is necessary to meet a required purpose i.e. function, asset or revenue. Codes can be used to have a speedy collection of accounts.
- Study the Technical Aspects – The predetermination of standards require to make a thorough analysis of technical aspects of the production process, to set the quantity standards i.e. standards in use of material and labour.
- Determination of Type of Standard – The standard may be current standard, basic standard or normal standard. The current standard may be ideal standard or expected standard. It is necessary to determine the type of standard to be adopted in the beginning of the standard costing system.
- Organization for Standard Costing – The success of standard costing system will depend upon the setting up of proper standards. For this purpose, a person or a committee is formed. Normally, the committee includes Production manager, Purchase manager, Marketing manager, HRD manager, Chief engineer and Cost accountant. The Cost accountant will act as a coordinator of different departments and supplies necessary information for determining standards and later on coordinates the costs of different departments.
- Setting of Standards – The standard for direct material, direct labour and overheads are fixed. It may be expressed in quantity and its monetary measurements in standard costs. The standards should be set up in a systematic way so that they are used as a tool for cost control.
- Modifications to Existing Financial Accounting System – It is more useful to modify the existing financial accounting system in collection of costs to suit the standard costing system, otherwise, it will be too much costly to have an independent standard cost accounting system.
- Training of Staff – The installation and implementation of standard cost system requires trained, qualified and experienced staff. A qualified and experienced Cost Accountant should be assigned with responsibility to achieve desired objectives of standard costing system and he should be capable of coordinating with top management, other departments, staff and workers.
- System Operating Costs – Sometimes the detailed cost system proposed to be installed may cause substantial installation and operating cost. The benefits from standard costing system should be more than the costs incurred on its installation and operation. The properly designed and installed system should meet the specific requirements of the concern and it should reduce all unnecessary paper work in the organization.
- Regular Comparison and Analysis – There should be a system of regular comparison of actual costs with standard costs and analysis of variances.
- Management By Exception Reporting – Only those variances which are outside certain tolerance limits are investigated and reported to management, thereby economizing on managerial time and maximizing efficiency.
- Management Support – Management should be convinced of benefits by installation and operation of a standard costing system. The basic objective of the system is to provide necessary information to the internal management for the purpose of cost control.
- Staff Support – The non-cooperation and resistance of other departments and staff can be overcome by explaining the simplicity and use of the standard cost system and ensure organization’s cost management and to increase its profitability.
11. Standard Cost and Estimated Cost: Distinction
Basis |
Standard Cost | Estimated Cost |
Predetermined Cost | It is a predetermined cost on a scientific basis taking into consideration all the factors relating to costs e.g., raw material consumption rate, labour efficiency, machine efficiency etc. | It is a predetermined cost based on past performance adjusted to the anticipated changes. No minute appraisal of each individual component cost. |
Application | It is ascertained and applied when Standard costing system is in operation. | It can be used in any business situation or decision making which does not require accurate cost. It is used in Budgetary control system and Historical costing system. |
Emphasis | Its emphasis is on what should be the cost. | Its emphasis is on the level of costs not to be exceeded. |
Purpose | It is used for analysis of variances and cost control purposes. | It is used in decision making and selection of alternative with maximum profitability. It is also used in price fixation and tendering. |
Variances | It is used as a regular system of accounts from which variances are found out. | The use of estimated cost as a statistical data only. |
12. Setting of Standards During Inflation
The inflationary tendency in the economy will cause fall in purchasing power of money thereby affects the accounting for real value. In inflationary conditions, the results shown in financial statements do not represent the correct view of activities carried on in the business concern. Any decision taken or estimates made without inflation would not be correct. Rate of inflation will have impact on future cash flows and profitability of the concern. Before any estimates made or standards set, the difference between money rate of interest and real rate of interest, the difference between them should be taken as rate of inflation.
The practical approach for adjusting inflation is as follows:
- Predict the cash flows in nominal rupees and use the nominal discount rate.
- Predict cash flows in real rupees and use a nominal discount rate.
13. Responsibility for Setting Standards
- Human Aspects – Human aspects of budgeting apply equally to standard costing.
- Behavioural Aspects – There are strong behavioural and motivational factors involved in this process.
- Involvement of Line Managers – The line managers who have to work with the standards must be involved in establishing them.
- Determination of Cost Centres – The cost accountant has to determine the units of products to be made by producing cost centres and work to be performed by service cost centres.
- Basis of Overhead Recovery – Overhead recovery rates has to be determined in advance and applied on that basis to product/cost centres.
- Determination of Standard overhead Rates – After application of service cost centres rates to production cost centres, a standard overhead rate has to be determined for each production cost centre.
- Responsibility Accounting – The purpose of setting standards is to fix yardsticks for measuring the performance of various activities and helps in responsibility accounting.
14. Standard Costing and Budgetary Control: Distinction
Basis |
Standard Costing | Budgetary Control |
Predetermined Cost | It is a system of accounting where predeter- mined costs are used for analysis of variances and control of entire organization. | It is a planning exercise made by the management in setting budgets for forthcoming period and analysis of actuals with the budgeted figures and corrective action is initiated if any deviations are identified. |
Scientific Determination | Standard costs are scientifically predetermined in respect of materials, labour and overheads. It is based on engineering & technical data. Standard costs are fixed for each unit i.e., standard hour, standard unit, standard labour mix, standard material mix etc. | Budgets are based on past performance adjusted to the anticipated changes in the future. It is a written plan covering projected activities of a firm for a definite time period. It is a financial measure of target and achievement. |
Quantitative/Monetary | Standard may be expressed both in quantitative and monetary measures. | Budgets are mainly expressed in monetary terms. |
Purpose | It is concerned with ascertainment and control of costs. | It is concerned with overall profitability and financial position of the concern. |
Variance | Any variance – adverse or favourable, is investigated. | It puts emphasis more on excess over the budget. |
Level of Cost | Its emphasis is on what should be the cost. | Its emphasis is on the level of costs not to be exceeded. |
Element of Cost | It is determined for each element of cost. | It is determined for a specified period. |
Control of Costs | It is related with the control of costs and it is more intensive in scope. | It is concerned with the operation of business as a whole and it is more extensive. |
Cost Performance | It is introduced primarily to ascertain the efficiency and effectiveness of cost performance. | It is introduced to state in figures as approved plan of action relating to a particular period. |
Whole or Departmental | Standards are usually limited to manufacturing activities only. | Budgets are set for all departments in an organisation. |
Projection | Standard cost is a projection of Cost accounts. | Budget is a projection of Financial accounts. |
Emphasis | Standard costs are used in tactical decisions like, product price fixation, computation of product cost, valuation of inventory etc. | Its emphasis on policy determination, achievement of goals, co-ordination of different departments and activities, delegation of authority and responsibility. |
15. Standard Costing and Budgetary Control: Interrelation
Usually budgetary control is operated with a system of standard costing because both systems are interrelated but they are not interdependent. One cannot have perfect and effective system of budgetary control without standard costing. Standard costing cannot be implemented without proper budgetary control system. The budgetary control system and standard costing are both supplementary and complimentary to each other. The standard costing is useful for MIS, profit planning, inventory control, product pricing, managerial decision-making, cost control etc.
Both standards and budgets are concerned with setting performance and cost levels for control purposes. They are similar in principle although they differ in scope. Standards are unit concept i.e. they apply to particular products, to individual operations or processes. Budgets are concerned with totals they lay down cost limits for functions and departments and for the firm as a whole.
16. Problems in Setting Standards
The problems to be faced in setting standards are as follows:
- Inflation – Deciding how to incorporate inflation into planned unit costs.
- Quality – Deciding on the quality of materials to be used, because a better quality of material will cost more, but perhaps reduce material wastage.
- Mix – Deciding on the appropriate mix of component materials, where some change in the mix is possible.
- Price Variations – Estimating materials prices where seasonal price variations or bulk purchase discounts may be significant.
- Behavioural Problems – Managers responsible for the achievement of standards might resist the use of a Standard costing control system for fear of being blamed for any adverse variances.
- Costs – The cost of setting up and maintaining a system for establishing standards.
17. Advantages and Limitations of Standard Costing System
17.1 Advantages
The benefits that can be reaped from adaptation of standard costing system are as follows:
- Aid to Management – It aids business planning, budgeting and managerial decision-making.
- Strengths and Weaknesses – Standard costing highlights areas of strengths and weaknesses.
- Formulation of Policies – Standard costing facilitates the formulation of production policies for various products by providing predetermined costs of each element of cost on the basis of engineering specifications.
- Coordination – It facilitates coordination between different functions such as purchasing, production, selling, accounting together while fixing standards.
- Measure of Performance – It acts as an yardstick to measure operating performance by comparing the variances and also assists in controlling cost by taking corrective steps.
- Increase in Efficiency – The setting of standards should result in the best resources and methods being used and thereby increase efficiency.
- Valuation of Inventory and Setting Wage incentive Schemes – Standard costs can be used to value stock and provide a basis for setting wage incentive schemes.
- Simplifies Book keeping – Standard costing simplifies book keeping, as information is recorded at standard, instead of a number of historic figures.
- Allocation of Costs – It helps to trace/allocate manufacturing costs to each individual unit produced.
- Management by Exception – Only those variances which are outside certain tolerance limits are investigated, thereby economizing on managerial time and maximizing efficiency.
- Immediate Control Action – As soon as material is issued from stores to production it can be compared with the standard material which should have been used for the actual production.
- Preparation of Tenders – When standard costing is in operation, estimation of product cost for tendering purposes becomes easy.
- Price Fixation – Price can be fixed based on standard costs provided there is no wide variation.
- Evaluation of Jobs – Introduction of Standard costing facilitates evaluation of jobs and introduction of incentives.
- Estimation of Costs – It facilitates the estimating of the cost of new products with greater accuracy and estimation of profit.
- Standardization – Standard costing helps in achieving standardization of products, operations and processes.
17.2 Limitations
The standard costing system is subject to the following limitations:
- Expensive – A lot of input data is required which can be expensive. The maintenance of the cost database is expensive.
- Repetitive Jobs or Processes – Standard costing is usually confirmed to organizations whose processes or jobs are repetitive.
- Accuracy of Standards – Unless standards are accurately set any performance evaluation will be meaningless.
- Environmental Uncertainty – Uncertainty in Standard costing can be caused by inflation, technological change, economic and political factors etc. Standards, therefore, need to be continually updated and revised.
- Motivation of Workforce – It may be difficult to set standards at a level which both motivates the workforce and achieves corporate goals.
- Difficult to Understand – Research evidence shows that overly elaborate variances are imperfectly understood by line managers and thus they are likely to be ineffective for control purposes.
- Possibilities of Error – Virtually all aspects of setting standards involves forecasting and subjective judgments with inherent possibilities of error and argument.
- Number of Variances – The usefulness of a number of variances relating to overheads, sales margins, mix and yield is questionable.
- Analysis of Historical Data – All forms of Variance analysis are postmortem on past events. Obviously the past cannot be altered so the only value variances can have is to guide management if identical or similar circumstances occur in future.
18. Reasons for Growing Importance of Overheads
There is an increase in overheads in the present scenario of industrialization, for which the following reasons can be highlighted:
- Industrial Needs – Standard costing originated as a control system designed to serve the industrial conditions of the time and proved to be a sound management tool.
- Change in Conditions – Conditions have changed dramatically and doubts have been raised about usefulness of standard costing in today’s industrial environment.
- Advanced Techniques – The world class manufacturers use computer assisted Advanced Manufacturing Technology (AMT) and Just-In-Time (JIT) production and purchasing methods.
- Change in Objectives – In the present day industrial environment, there is a constant drive for
-
- improvement and excellence,
- elimination of all forms of waste,
- move towards zero defects and inventories,
- production according to demand rather than for stock.
- Changes in Cost Patterns – As a consequence of the latest developments in production systems, there have been major changes in cost patterns. These can be summarized thus:
-
- Direct labour now constitutes only a small proportion of costs, typically 5 to 15%, in modern factories.
- Most costs are now fixed in the short-run, including labour. In many factories, materials and power costs are the only variable costs.
- Overheads are a much higher proportion of total costs and need to be monitored and controlled much more closely than in the past.
19. Non-Compatibility of Standard Costing with Activity Based Costing
The traditional Standard costing system is not compatible with Activity based costing system due to the following reasons:
- Cost Pattern – Manufacturing costs represents a low proportion of total cost.
- Ignorance of Selling costs – Product selling and distribution expenses are ignored for product costing purposes.
- Overheads – ABC system addresses treatment of all overhead related costs linking with cost drivers and cost pools.
- Material Cost – Material cost will be treated as direct costs both in ABC and Standard costing system, except that all costs incurred in bringing the product to its current state and location will be included in ABC system.
- Labour Cost – Labour, as a basis for assigning manufacturing overhead, is irrelevant as it is significantly less than overhead and many overheads do not bear any relationship to labour cost or labour hours.
- Cost of Technology – The cost of technology is treated as product cost and consequently expressed on a straight line basis, irrespective of use.
- Service Costs – Service related costs like professional services, banking services, insurance services have increased considerably.
- Customer Costs – Customer related costs like finance charges, discounts, selling and distribution costs, after sales service costs etc. are not related to product cost object. Customer profitability has become as crucial as product profitability.
- Information Systems – Direct labour is also replaced to some extent by Information technology and systems. These costs are treated similarly to organizational overheads and not related to products or other cost objects, such as customers.
- Time Costs – Costs affected or driven by time (interest & inflation) have increased significantly.
- Short-Term Focus – Short-term focus of financial year (12 months) is still intact, yet most products and technologies have life cycles exceeding many accounting periods.
- Intensity of Competition – Increased competition brought about by increased productivity, economies of scale, better communication technology, improved transportation, better marketing skills, increased marketing costs.
- Product Mix – Greater variety and diversity of products are not taken into consideration in traditional systems.
- Customer Driven Market – The current market calls for production of goods and rendering of services desired by the customer/client, and not those thought proper by the supplier.
20. Behavioural Considerations in Standard Costing
- Alignment of Individual Goals with Organizational Goals – Standard costing system should be developed in such a way that individuals are encouraged to behave in a manner which is consistent with overall goal of the organization.
- Goal Congruence – There should be a goal congruence between the personnel goals and the organizational goal. Performance measures should encourage goal congruence.
- Motivational Approach – Specific quantitative targets have a strong motivational approach, but careful consideration should be given to the degree of difficulty represented by target figures.
- Participation – There should be appropriate participation of managers in preparation of budgets.
- Flexible Attitude – This may result in bias and the same can be avoided by taking a flexible attitude while setting standards.
21. Meaning of Variance Analysis
21.1 Variance
It is the difference between planned, budgeted or standard cost and actual costs and similarly in respect of revenues. It represents a deviation of the actual result from the standard result. This should not be confused with the statistical variance which measures the dispersion of a statistical population.
21.2 Variance Accounting
It is a technique whereby the planned activities of an undertaking are quantified in budgets, standard costs, standard selling prices and standard profit margins. The differences between these and the actual results are compared. The procedure is to collect, compare, comment and correct.
21.3 Variance Analysis
It is the analysis of variances arising in a Standard costing system into their constituent parts. It is the process of analyzing variances by subdividing the total variance in such a way that management can assign responsibility for below the standard performance. It is the analysis and comparison of the factors which have caused the differences between predetermined standards and actual results, with a view to eliminating inefficiencies. It is an exercise, which involves efforts to isolate the causes of variances in order to report to management those situations, which can be corrected and controlled by timely action. There can be cost variances, profit variances, sales variances and operational and planning variances. A suitable analysis will reveal that some of the variances are controllable, while others are uncontrollable. By analyzing variances, origin and the causes of variances can be traced so that steps can be taken to reduce them. The conventional variance analysis is a postmortem exercise.
A detailed analysis of controllable variance helps the management to ascertain:
- amount of variance,
- the cause of variance,
- the person responsible for its occurrence, and
- the corrective action to be taken.
21.4 Methodology
The methodology in implementation of variance analysis are as follows:
Step 1: Standards of performance for each activity or each segment of cost (material, labour, overhead) should be set.
Step 2: Setting of standards and construction of a budget based on them.
Step 3: Organization structure with responsibility centres that can be identified with standard costs should be defined.
Step 4: An information system to compile data on actual outcomes should be built up for comparison and analysis of variances.
Step 5: Comparison of actual with budgeted outcomes.
Step 6: Factoring the variance into individual components and investigation of the significant differences. Step 7 The objective is to help ‘management by exception’ to identify the cause for taking corrective action.
21.5 Cause of Variance
There are many possible causes for cost variances arising due to efficiencies and inefficiencies of operations, errors in standard setting, changes in exchange rates etc. The following are the important causes for variances:
- Implementation Deviation – It results from a human or mechanical failure to achieve an attainable income.
- Prediction Deviation – It results from errors in specifying the parameter values in decision model.
- Measurement Deviation – It arises as a result of error in measuring the actual outcome.
- Model Deviation – It arises as a result of an erroneous formulation in a decision model.
- Random Deviation – It is due to chance fluctuations of a parameter for which no cause can be assigned.
21.6 Classification of Variance
- Variance of Efficiency – These variances arise due to the effective or ineffective use of materials quantities, labour hours, once actual quantities are compared with the predetermined standards.
- Variance of Price Rates – These variances arise due to change in unit material prices, standard labour hour rates and standard allowances for overheads.
- Variance Due to Volume: These variances arise due to the effect of difference between actual activity and assumed level of activity, when the standard was set.
Disclaimer: The content/information published on the website is only for general information of the user and shall not be construed as legal advice. While the Taxmann has exercised reasonable efforts to ensure the veracity of information/content published, Taxmann shall be under no liability in any manner whatsoever for incorrect information, if any.
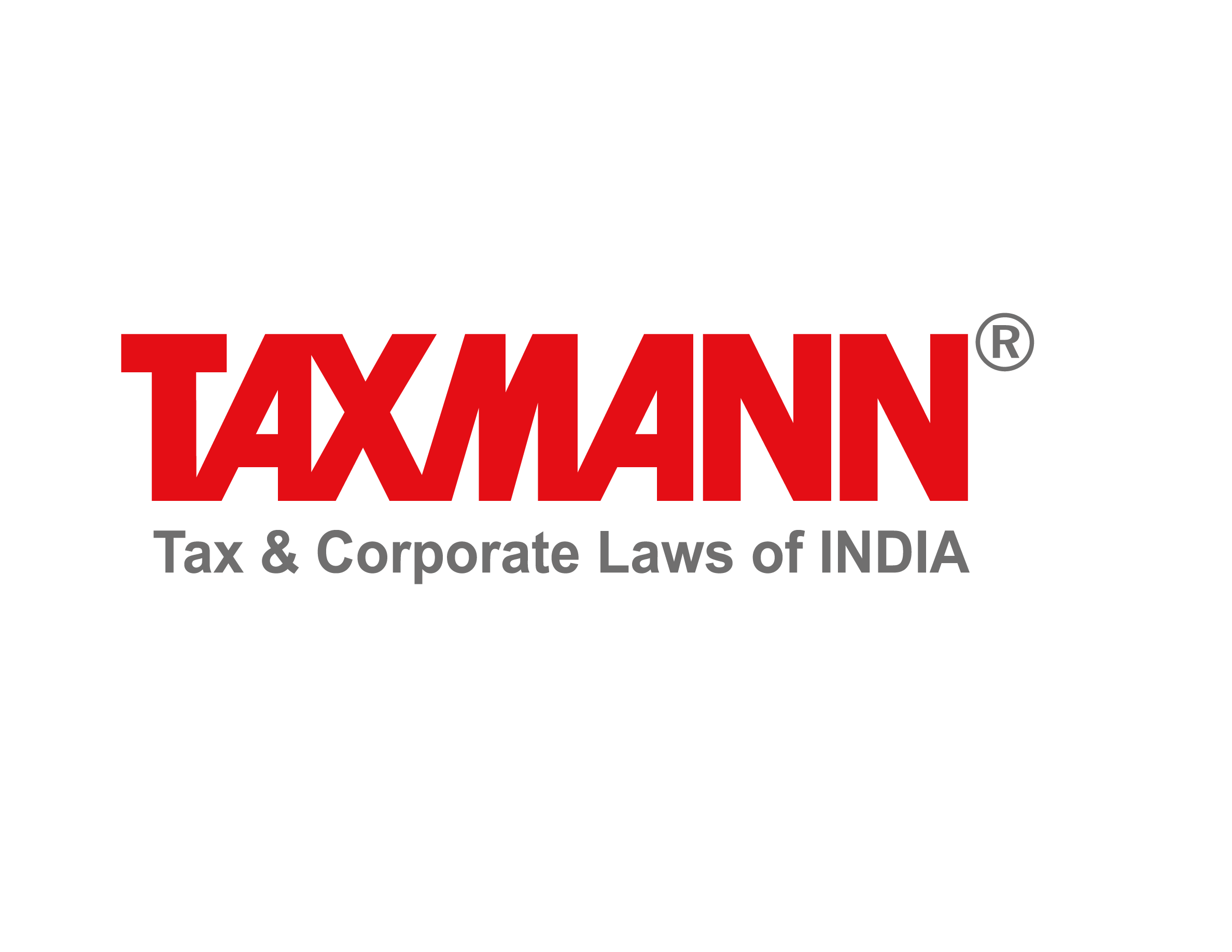
Taxmann Publications has a dedicated in-house Research & Editorial Team. This team consists of a team of Chartered Accountants, Company Secretaries, and Lawyers. This team works under the guidance and supervision of editor-in-chief Mr Rakesh Bhargava.
The Research and Editorial Team is responsible for developing reliable and accurate content for the readers. The team follows the six-sigma approach to achieve the benchmark of zero error in its publications and research platforms. The team ensures that the following publication guidelines are thoroughly followed while developing the content:
- The statutory material is obtained only from the authorized and reliable sources
- All the latest developments in the judicial and legislative fields are covered
- Prepare the analytical write-ups on current, controversial, and important issues to help the readers to understand the concept and its implications
- Every content published by Taxmann is complete, accurate and lucid
- All evidence-based statements are supported with proper reference to Section, Circular No., Notification No. or citations
- The golden rules of grammar, style and consistency are thoroughly followed
- Font and size that’s easy to read and remain consistent across all imprint and digital publications are applied